Before (改善前)
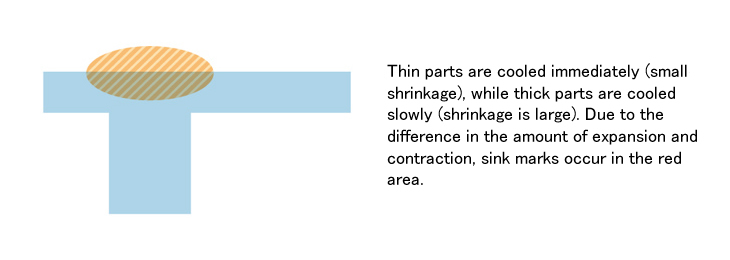
If the difference in wall thickness is large in plastic injection molded products, the cooling speed of the thick part is slower than that of the thin part, so the shrinkage of the plastic resin increases and sink marks are more likely to occur. For example, as described above, in plastic injection molding where there is a large difference in thickness, the thicker part is cooled more slowly than the thinner part, it results sink marks are more likely to occur in red areas. Because of this, since the yield rate of defective products increases, the yield tends to be worse.
V
After (改善後)
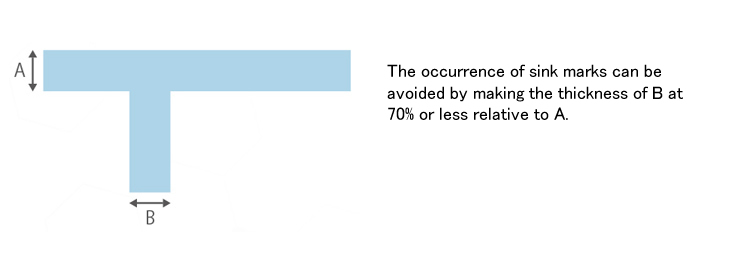
By changing the thickness of plastic injection molded products, the occurrence of sink marks can be suppressed. By changing the thickness of B above to 70% or less of the thickness of A, it becomes possible to avoid sink marks. However, care must be taken because if it is too thin, there will be problems with strength. If it is difficult to change the wall thickness due to the intended use, change the gate position to adjust the filling speed and cooling speed for each part, and select a plastic resin in consideration of the material shrinkage to minimize the occurrence of sink marks.
POINT(要約)
Methods to make sink marks in plastic injection molded products less noticeable include coloring the material with white or embossing the mold. White reflects light, and embossing also reflects light irregularly, making sink marks less noticeable. These are measures for appearance only and are not product design changes or mold design changes, but are methods that may be effective as first aid measures. However, when producing high-quality plastic injection molded products by suppressing the occurrence of sink marks fundamentally, it is necessary to consider design changes as in this case.