Before (改善前)
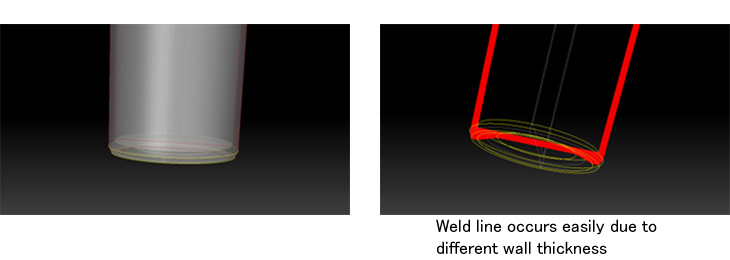
This is a case that the thickness of the side and bottom surfaces are different with round plastic injection molded container. Normally, when manufacturing a round container by plastic injection molding, it is manufactured using a pin gate from the outside of the bottom. However, if the thickness of the side and bottom surfaces of the round container is different, the flow of the plastic resin to be filled at the point where the thickness changes will change, making it easier to form a weld line, making the appearance worse, It leads to quality deterioration.
V
After (改善後)
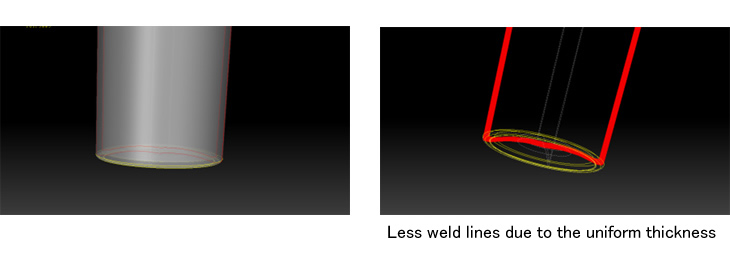
When manufacturing a round plastic injection molded container, it is possible to manufacture round plastic injection molded containers with no weld line and nice shape by designing to be minimize the difference in thickness between the side and bottom surfaces (preferably make the thickness of the side and bottom surfaces the same). By minimizing the difference in thickness between the side and the bottom, the flow of the plastic resin to be filled is prevented from changing suddenly, and R corners with nice shape can be created.
POINT(要約)
In the case of plastic injection molding, weld lines are likely to occur at the point where the filling resin joins. Although since uniformed wall thickness and uniformed flow distance make the temperature of the plastic resin will be the same, less weld lines can be expected, however, when the wall thickness or distance changes like a round container, it is need to use caution. If there is no problem in the function, it is possible to prevent the occurrence of weld by changing the design from the product design and mold design stages and making the change to eliminate the thickness difference as described above.